Controlling costs: how a meal service automated its packaging management
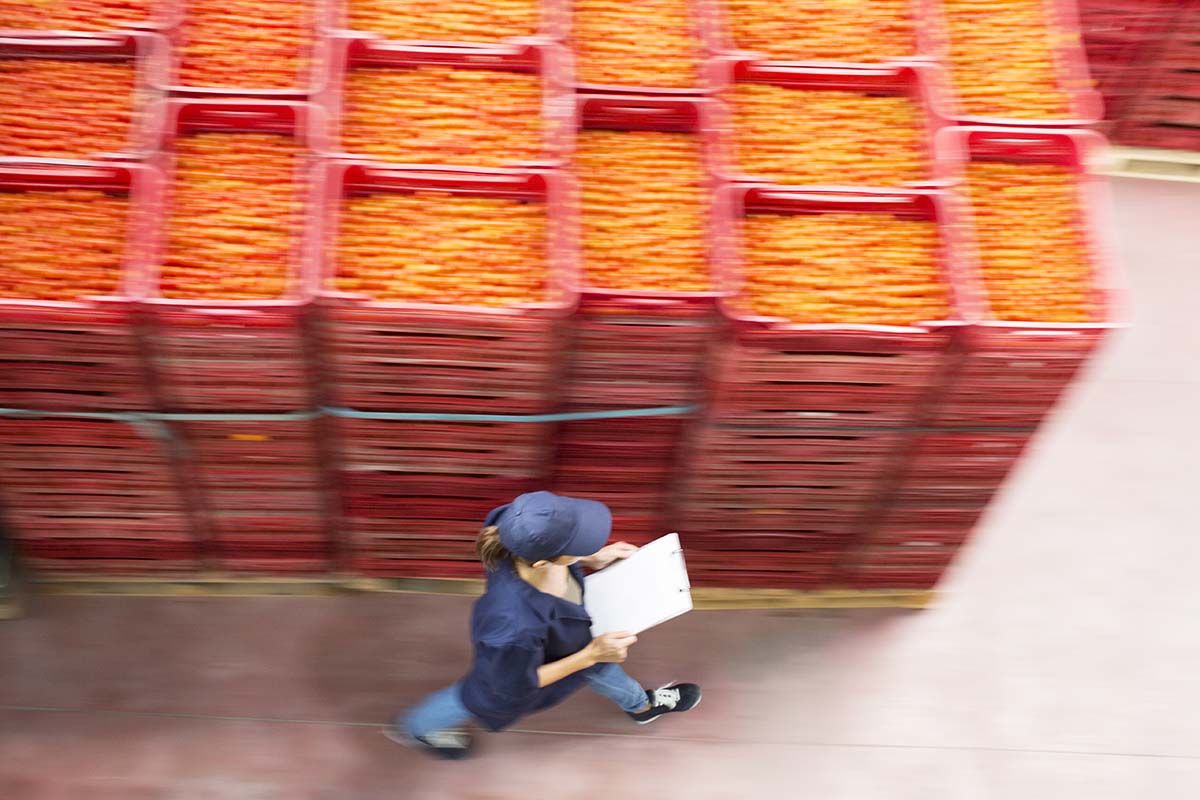
An international meal kit delivery service was reaching the limits of its packaging registration. Costs, particularly deposits, were spiralling out of control and packaging management was becoming a huge logistical and financial challenge. In this user case we will show you how they solved the problem.
You know them: those handy meal kits with fresh ingredients and recipes. They are delivered to your door so you can put a delicious meal on the table without any fuss. Sounds simple, but behind this service is a huge amount of reusable packaging. Just think of the number of crates, pallets and trolleys needed to transport all the ingredients from the grower or manufacturer to the meal supplier. Managing this is a logistical challenge that can turn into a nightmare if you don't keep it under control. Reaching the limits of its packaging records, this international meal delivery company found the solution in PackControl.
With thousands of orders every day, MealService* has huge amounts of reusable packaging in circulation. Until recently, incoming and outgoing crates, pallets and trolleys were mostly processed manually via Excel files. The result? Limited insight into packaging whereabouts, challenging audit of deposit invoices, and high costs from losses and inefficient usage.
The primary issue for the company were the deposit invoices from suppliers. MealService noticed that the amounts on the invoices often differed from the actual number of items received. While they initially thought these discrepancies were caused by a miscount at goods receipt, it turned out that the problem lay primarily with the suppliers. They were invoicing based on production assumptions and had no insight into the real number of packaging items shipped. Their assumptions often proved to be incorrect.
MealService decided to switch to PackControl, the packaging management system that can automate and complete the entire packaging registration process. This tool allows the company to effortlessly register all packaging items at every step of the process, from delivery by suppliers to item returns and cost settlement.
Within six weeks, the company achieved its goal of reducing deposit variance
The main issue for the company lay with the deposit invoices from suppliers. MealService found that the amounts listed on these invoices often didn’t match the actual number of items received. At first, they assumed the discrepancies were due to errors during goods receipt. However, it soon became clear that the problem stemmed primarily from the suppliers, who were invoicing based on production estimates rather than the actual number of packaging items shipped. These estimates frequently turned out to be inaccurate.
The introduction of PackControl marked a significant change for this meal kit service. Upon receiving supplies, MealService emails each supplier with a signed packing slip and the number of packaging items delivered, along with the anticipated deposit values on the invoice. Should the supplier find discrepancies in the numbers, they have five days to report them through the online ticket system.
The implementation of this new automated system has brought about a substantial positive impact. In just six weeks, MealService successfully minimized the discrepancies between the deposit amounts on invoices and the actual items received. Considering that these discrepancies often involved H1 pallets valued at €70 each, the savings achieved were significant.
Do you use returnable packaging in your business and find it challenging to manage? If so, the story above illustrates how digital solutions can assist you. With PackControl's packaging management system, you can move away from manual lists and avoid discovering later that you've been overpaying. You gain control over your packaging processes, reduce costs, and operate more sustainably.
Would you like to know how PackControl can optimise your packaging management? Contact us and discover the possibilities!
* Fictitious name, images do not represent the company in the story.